Table of Contents
Solid State Technology
Year 2001 Issue 9
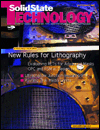 | DEPARTMENTS
Editorial Is chipmaking skill still a differentiator?
Winning isn't easy in the tough, rapidly evolving semiconductor market. Many of the new applications call for specialized chips to maximize performance and minimize space and power requirements.
Market Watch Infrastructure matures as Flip chip takes off
Flip chip technology has already expanded in two major areas: one driven by the high performance needs of microprocessor, ASIC, and high-end DSP devices, the other driven by form factor, where die sizes are small and packaging cost must be as minimal as the package itself.
World News World News
Worldwide Highlights; USA; Japan; Europe; Asia Pacific...
Tech News CaF2 birefringence workshop reaches consensus
Attendees of a worldwide workshop on "intrinsic birefringence" in CaF2 a key material for future 157nm lithography agreed that this phenomenon does not constitute a showstopper. One International Sematech workshop participant at the Semicon West conference observed, however, that "the problem is worse than they are admitting...
Show Report SEMI WEST SHOW REPORT: Attendees challenged by economy
What a year! Soaring sales, unprecedented expansion, and a seemingly infinite tech-driven economy gave Semicon West a party atmosphere, full of hope, optimism, and plans for future prosperity.
The year, unfortunately, was 2000.
New Products New Products
RTP system for 300mm by Axcelis Technologies Inc., Beverly, MA; Litho cluster for wafer level packaging by Karl Suss, Munich, Germany; Submicron prober by MFI Technologies, San Jose, CA; Point-of-use pump by Alcatel Vacuum Technology/Applied Materials Inc., Annecy, France...
Calendar Calendar
A listing of industry events, covering September to November 2001.
|
|
FEATURES
Cover Article A method for evaluating RETs for advanced masks
To evaluate the efficacy of various resolution enhancement techniques (RETs), a method is proposed that gathers aerial intensity images from real masks under actual illumination conditions. Correlations to wafer-generated process latitudes are then established.
Lithography Optimal insertion points for OPC and PSM in design flows
To reexamine the optimal insertion points for OPC and PSM, pattern data are manipulated and presented both in the context of the litho/design flows and as a set of transformations between discrete states. Although OPC retains its insertion point at layout verification, PSM represents a more complicated situation.
Implantation Implanter, RTP system issues for ultrashallow junction formation
Only when both ion implantation and rapid thermal annealing are tightly controlled can successful ultrashallow junction production be performed. An implanter's sensitivities are to dose variation, energy, and elemental contamination. These can be controlled with advanced software-driven control systems, precision power supplies, and accurately designed beamline geometry.
Thin Film Technology Advanced magnetic recording media for high-density data storage
n current magnetic recording media the signal-to-noise ratio needed for high-density recording is achieved by statistically averaging a large number of weakly interacting magnetic grains per recorded bit. Traditional engineering of magnetic media to achieve higher recording densities involves reducing the grain diameter and film thickness, but this approach is increasingly limited by instabilities due to thermal fluctuations.
Contamination Control Purged gas purification for contamination control of DUV stepper lenses
The measurement and control of optical lens contamination by airborne molecular contaminants has not received much attention. To control and enhance light throughput, the universal solution is to purge optical parts with ultra-high-purity gases [1].
Cmp Tuning the process flow to optimize copper CMP
CMP is considered the biggest process challenge for the new generation of copper-based chips. Problems that arise here ultimately affect chip performance. However, chip manufacturers can significantly improve results by optimizing pre- and post-CMP steps. This article looks at copper CMP in the context of the entire interconnect process flow, examining steps that can be taken to make CMP easier in next-generation device processing.
Industry Insights How clean can we get?
Today, we are basically without good baselines and specifications for the quality of air in cleanrooms. Most fab engineers do not know the level, type, or quantity of contaminants that exist in their cleanrooms or what these should be by product type.
| |
COPPER-LOW-K-DIELECTRICS
Low K Dielectrics A new class of insulating materials: Emergence of ultralow-k
As transistor scaling extends below the 0.18?m technology node, propagation delays associated with interconnects begin to bottleneck the operating speeds of transistors. New interconnect materials are needed to reduce the RC time constant associated with the delays.
Cmp Advanced processing: CMP of Cu/low-k and Cu/ultralow-k layers
Cu/low-k interconnect technology has become a critical technology for 0.1µm and sub-0.1µm IC device manufacturing due to the increased device speed, enhanced electromigration resistance, and improved scalability it affords.
Metrology Picosecond sonar used to characterize copper processes
During full production, tight process control becomes the priority. With the move to copper, each step must be optimized to maintain high yields. The addition of 300mm increases the cost of process excursions; a finished 300mm wafer is expected to be 1.5 times as expensive as a comparable 200mm wafer [1, 2].
Cu Low K Techniques to improve Cu/low-k integration
The explosion in Internet usage and wireless communications has driven an unparalleled demand for cost-competitive, high-performance computing, communications, and information technology products. The challenge for the semiconductor industry in meeting this hunger for new and more sophisticated products is to bring new technologies into high-volume manufacturing in the shortest time and with the minimum development and manufacturing costs.
| |
|