Chris Bailey, VP Systems and Solutions, Edwards Vacuum, Burgess Hill, U.K.
Many wafer processes use only a small proportion of the gases that pass through the process chamber and discharge the rest, often after considerable cost and effort to mitigate any negative environmental impact. Recovery and recycling of most materials is possible, but is it worth it? The answer depends on value and cost. Cost includes both the cost of the technology and potential cost resulting from increased risk and system complexity. Value depends on many factors related to the specific problems to be solved, such as material scarcity, supply reliability, logistics, cost differential between recycled and purchased material, and environmental benefits. We will briefly review the benefits and costs that must be considered with an eye toward identifying circumstances that might justify recycling and recovery.
Benefits
Recycling can provide a reliable supply at a stable, predictable cost. The primary consideration is the cost differential between new and recycled material. New material will have a baseline price set by the inherent cost of production, though the price actually paid will be influenced by market forces of supply and demand. Some gases are abundant in nature and others inherently scarce. The price of abundant gases is driven primarily by separation and purification costs. In some cases, it is less expensive to simply extract a gas from the atmosphere on-site than to purchase or recycle it. Inherently scarce materials will never become more plentiful and their prices are, therefore, more susceptible to changes caused by swings in demand. When increased demand can be predicted, for instance, based on the wide spread adoption of a new application, it may be prudent to consider recycling in anticipation of increasing prices. The risk and potential cost of price volatility caused by geopolitical or natural events that are difficult or impossible to predict must also be factored into a cost analysis. Recycling gases can directly reduce fab emissions and the load on (and cost of) downstream abatement equipment. Finally, the cost of transport and local storage for new material must also be considered in the analysis.
Costs
The costs of recycling begin with the initial investment in equipment and ongoing operating expenses. Point-of-use systems will also carry a cost for additional space in the sub-fab. Generally, equipment in the sub-fab is also expected to fit within the “shadow” of the fab system it supports. Although recycling largely eliminates the risk of supply interruptions caused by external events, it adds the risk of interruption caused by failure of the recycling system. The risk of wide spread contamination may also increase compared to batch supplies where contamination is typically restricted to a specific container or lot. There are additional risks to the safety of fab personnel and the surrounding community associated with the handling and storage of hazardous gases. Clearly, a thorough risk assessment must be part of any cost analysis.
Recycling technologies
Costs are primarily determined by choices made in two areas, technology and complexity. The most important drivers on the technology side are the type of material to be recovered, other materials in the stream, the purity required, and the process duty cycle. Typically, recycling includes separating wanted and unwanted components of the gas stream, pressurizing the recovered gas for storage and reuse, and purifying the gas to the required level. Many technologies are available, including:
Separation
Adsorption – either the wanted or unwanted material is selectively attracted to the surface of an adsorbent. The adsorbent will eventually become saturated and require replacement or regeneration, during which adsorbed material is released to allow the adsorbent to be reused.
Membrane – relies on pressure (concentration or chemical potential) gradients and selective diffusion across a membrane to achieve separation.
Electrochemical – gases that have reversible redox reactions, e.g. H2 <=> 2H+ + 2e-, can be separated electrochemically under ambient pressure and temperature conditions in a fuel cell like device. The gas is electrochemically converted to an ion at an electrode, transported across an ion-conductive membrane by a potential gradient, and reconverted to the gas at the other electrode.
Phase change – uses differences in phase change temperatures to selectively remove components from the stream (e.g. distillation).
Pressure/temperature swing adsorption – is a variation on adsorption that exploits the tendency of different gases to adsorb more strongly at elevated pressures or temperatures. Vacuum swing adsorption is similar but swings between sub-atmospheric and atmospheric pressures.
Chromatography – separates components in a mobile phase (the gas) based on differences in their interactions with a stationary phase (a liquid or solid material) as they travel through it.
Pressurization
Mechanical – mechanical pumps use a wide variety of mechanisms to compress the gas.
Electrochemical – similar to electrochemical separation, gas, ionized at an anode, is driven across an ion-conductive membrane to a cathode. Multistage compressors, which link many membrane-electrode assemblies (MEA) in series can achieve very high pressures (> 1000bar). They are noiseless, scalable, modular and energy efficient.
Purification
Membrane – used similarly to membrane separation, relying on different diffusion rates between the recycled gas and impurities.
Getter – a getter is a reactive material that interacts with contaminants chemically or through adsorption to remove them from the recycled gas.
System complexity
Costs and risks typically go up with increasing system complexity. The primary driver of system complexity is the difficulty of the recycling process. In some cases, a single stage process will be sufficient, other cases will require multiple steps. Other drivers include requirements for:
Scalability – does the system need to support multiple tools and different processes?
Traceability – can the effects contaminants and sub-standard materials be isolated and contained to prevent wide-spread impact?
Duty cycle – is the supported process intermittent or continuous? Are multiple synchronized recycling systems needed to support continuous demand? How much storage capacity is needed to buffer and synchronize intermittent demand? Will the frequency of the duty cycle accommodate any settling or stabilization requirements in the recycling system?
Maintenance and regeneration – are idle periods in intermittent processes sufficiently long to permit maintenance and regeneration?
Availability, redundancy and backup – is the recycling system reliable enough to meet the uptime requirements of the supported process?
Hazard assessment – what risks to fab personnel and the local population are associated with handling and storage of hazardous materials?
Facilities – is space available in the sub-fab or will the system be housed externally?
System complexity options fall into two major categories (table 1): single chamber or area (multiple tool) support and open-loop (process waste sent to an offsite refiner) or closed-loop (on-site recycling). A single chamber approach is well suited to continuous processes with constant flow rates and unchanging process reactions. It scales easily to additional systems. An area approach can smooth out the flow from multiple discontinuous process tools and accommodate changes in output concentration caused by varying process reactions. A closed-loop system eliminates supply logistics problems and avoids the need to arrange outbound transport or find a refiner that will accept waste material. An open-loop system provides a supply that is independent of fluctuations in flow rate, shifts the burden of purification to the refiner, and provides batch-level containment of contaminants.
Single Chamber | Area | |
Closed |
Supply matches demand Scalable Containment of contamination Solves logistics concerns
|
Multiple asynchronous chambers flatten demand from discontinuous applications
|
Open |
Purity assured by refiner
|
Amortization of costs across multiple tools Purity assured by refiner
|
Table 1 Compares open-loop, closed-loop, single chamber and area system design options
Examples
Edwards has designed and built recycling systems for a variety of applications, including: CF4, F2, Xe, SF6, and H2. Of these, F2, Xe, and H2 are the perhaps the most interesting, for very different reasons.
Fluorine
F2 is relatively abundant but highly reactive. It is widely used for chamber cleaning. The impetus for this development project was a shortage of NF3 caused by an increase in demand and a supply hiatus that turned out to be temporary. The system was designed to recover F2 used to clean a PECVD chamber. The effluent gas stream contained F2 and SiF4. During the cleaning phase, exhaust flow was diverted through a pressure swing absorber (PSA), which collected SiF4 and returned F2 to the process chamber. During the deposition phase, the PSA was regenerated, with SiF4 removed by the process pump and abated downstream (FIGURE 1). The system required careful synchronization based on signals from the process tool. It was crucial that the ratio of deposition to cleaning was sufficient to allow complete regeneration of the PSA. Interestingly, we found that on-site generation would have provided a simpler and more cost effective solution. Ultimately the problem was solved when the NF3 supply chain was restored.
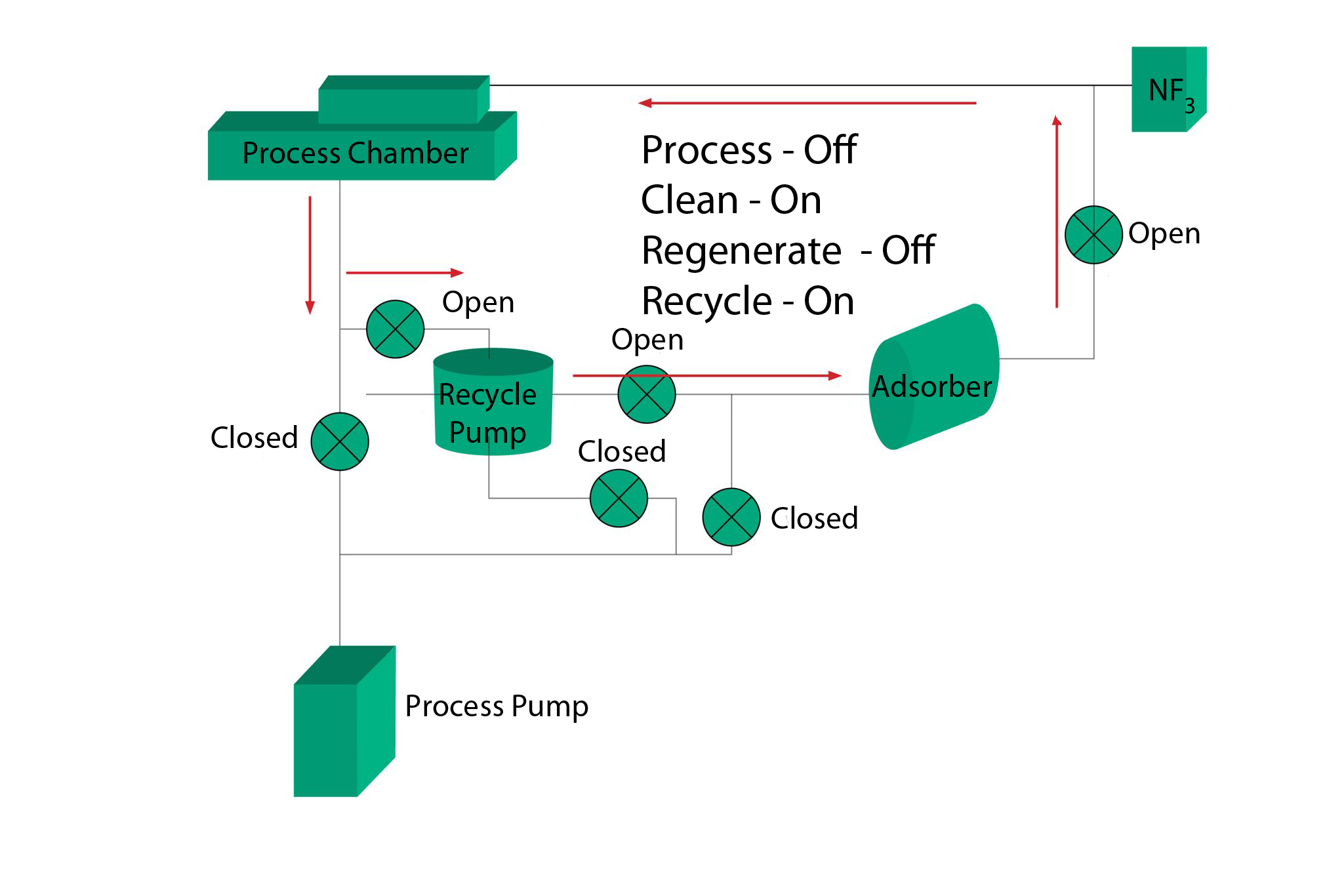
FIGURE 1. Fluorine recycling from a PECVD system requires careful synchronization with deposition and clean cycles to permit regeneration of the PSA adsorbent.
Xenon
Xenon is very rare and very stable, both of which is why it is recommend for recycling. Although Xenon currently has no mainstream applications, it has interesting properties that justify continuing investigation, including its behavior in plasma where its use has been considered to support reduced energy ion etch to extend hard mask life. Xenon was also considered for use in EUV light sources. Xenon’s scarcity virtually mandates recycling, especially if it were to become part of a widely adopted process. In the etch application, the primary hurdle was separating it from other components in the waste stream. Ultimately, the solution was an integrated, self-contained system that included a vacuum pump, a chromatography separator, a membrane separator and a backup supply reservoir (FIGURE 2).
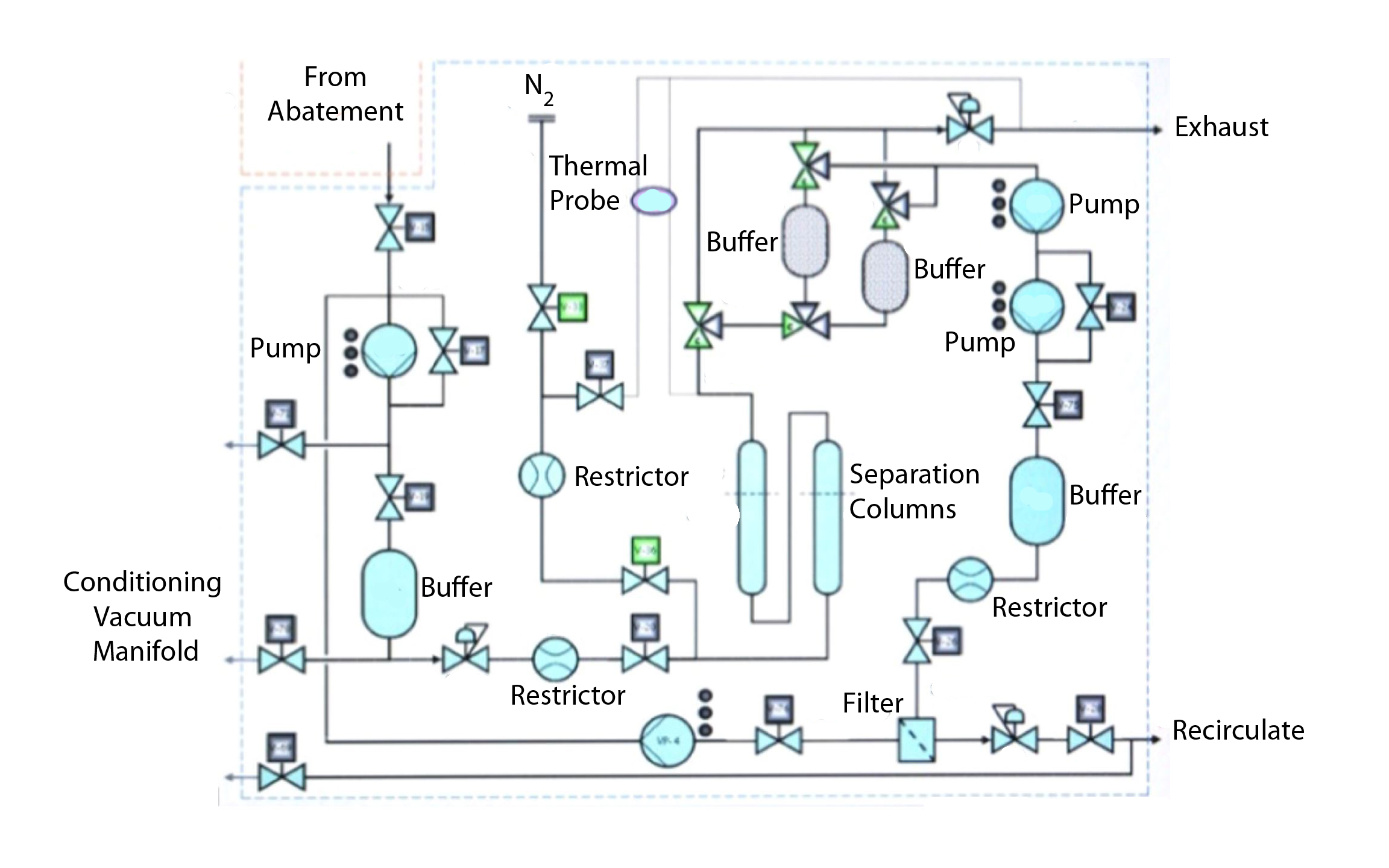
FIGURE 2. Xenon’s scarcity and stability make it a strong candidate for recycling should it become widely used. The system shown here — schematically combined chromatography and membrane separation technologies in a self-contained enclosure that included pumping and back-up storage.
Hydrogen
Hydrogen is at the other end of the scarcity/abundance scale from Xenon. It is the most common element in the universe and readily available in some form almost anywhere. It is relatively stable, except that it is highly flammable. The primary recycling challenges are related to safe handling and storage. Hydrogen is already used in many semiconductor manufacturing processes, but the adoption of EUV lithography is expected to dramatically increase hydrogen consumption. EUV light sources use very high hydrogen flows, hundreds of liters per minute, to remove scattered debris that would otherwise contaminate expensive collection optics. The debris originates from Sn, which is injected into the source and irradiated by a high-power laser to create a plasma that emits EUV light. Even without EUV lithography, leading edge fabs may consume as much as several normal cubic meters (Nm3 = 1000 standard liters) of hydrogen per wafer, equating to hundreds of Nm3 per hour per fab. Some estimates have that rate doubling with the adoption of EUV lithography. [1]
Given adequate measures to address the safety risks posed by its flammability, hydrogen is a good candidate for recycling (FIGURE 3). EUV lithography systems are very expensive ($100M+) and therefore intolerant of downtime. Good recycling system design with adequate provision for redundancy and backup can assure a reliable local source. Hydrogen is consumed in a steady continuous flow. Its recovery involves relatively simple chemistry, and well-proven electrochemical technologies exist for separation and compression. A PSA can be used to remove added water.
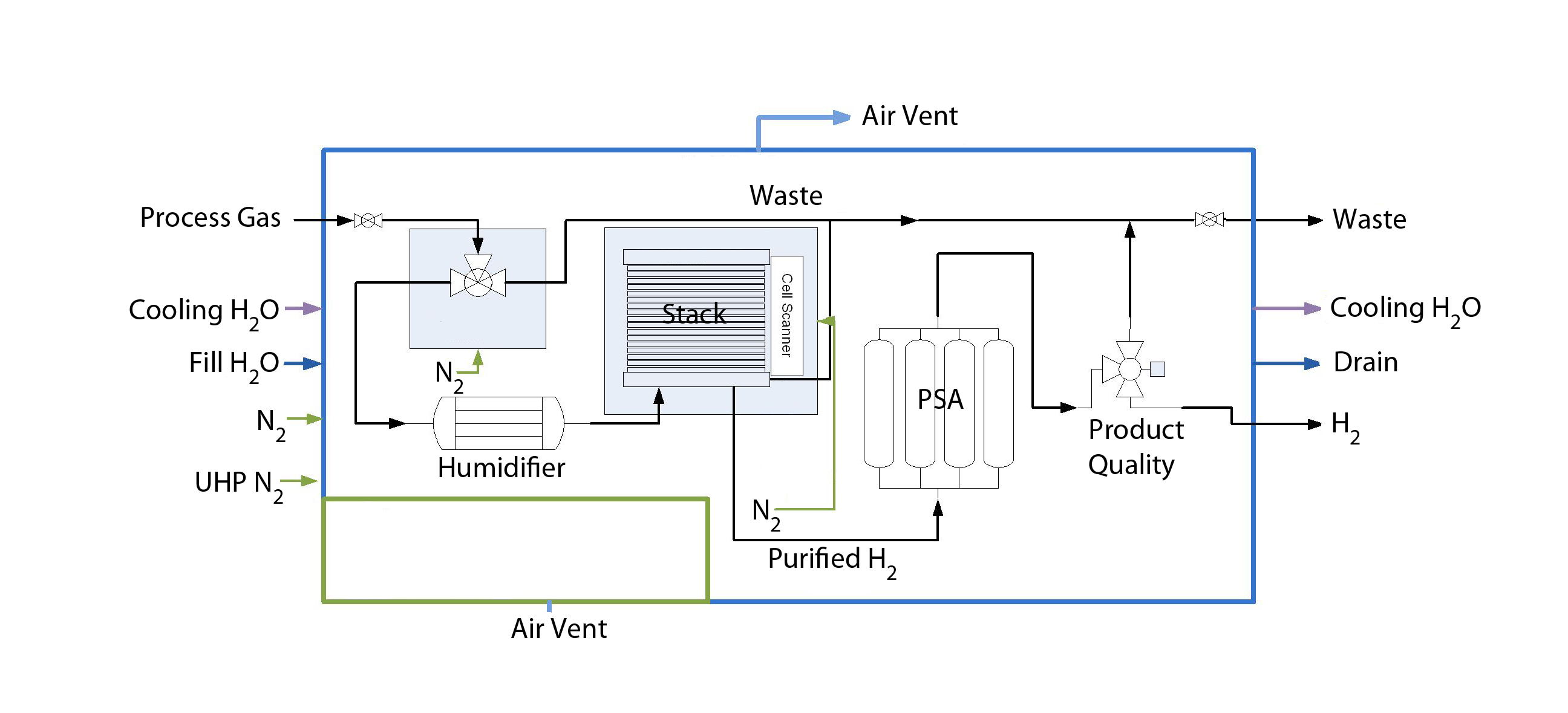
FIGURE 3. Hydrogen recycling may be justified by the dramatic increases in consumption anticipated with the adoption of EUV lithography. Its simple chemistry and continuous flow rate make it a good candidate, in spite of its relative abundance. The primary challenge is the safety risk posed by its flammability.
Conclusion
Many semiconductor manufacturing processes use only a small fraction of the materials supplied to the process chamber. While we have focused here on recycling gases, it is worth noting that some metal precursors, ruthenium, for example, may also be candidates for recovery and recycling for similar reasons. Proven technologies exist for recovering and recycling unused materials. The value of recycling depends primarily on the cost differential between new and recycled material. The cost of recycling is driven primarily by the technology required and the complexity of the recycling system. Steady state processes and simple chemistries are likely to be the most viable candidates. Discontinuous processes and complex chemistries increase system complexity and add cost and risk. Any consideration of recycling must take a systems-level approach, thoroughly considering all predictable and potential costs, including risks of downtime, contamination and safety. Though recycling of process gases is not now common, there is much to recommend considering it, from both economic and environmental points of view. It represents the kind of out-of-the-box thinking that has contributed again and again to our industry’s impressive history of innovation and success.
References
- Stockman, P; EUV Lithography Adds to Increasing Hydrogen Demand at Leading Edge Fabs; Solid State Technology, 3/22/2018, vol.61, issue 2
Editor’s Note: This article originally appeared in the November/December 2018 issue of Solid State Technology.