May 31, 2011 — The US Department of Energy’s Lawrence Berkeley National Lab, in partnership with the University of California at Berkeley, are working on substrates that best preserve graphene’s intrinsic nano properties. So far, the groups led by Michael Crommie and Alex Zettl, Materials Sciences Division, Berkeley Lab and UC-Berkeley physics professors researched graphene’s interaction with a boron nitride substrate.
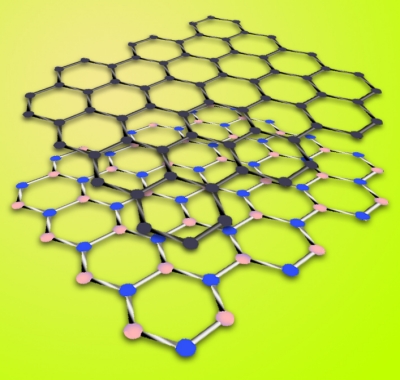 |
Figure 1. Graphene (top layer) is a hexagonal "chicken wire" arrangement of carbon atoms. Hexagonal boron nitride is a similar arrangement of boron and nitrogen atoms; its lattice constant is just 1.7% larger than graphene’s.
|
Graphene’s intrinsic properties — very high electron mobility, very low resistivity — are best studied on suspended graphene, notes Régis Decker, a former postdoctoral fellow in the Crommie group, now at the University of Hamburg, Germany, and lead author of the results published in Nano Letters. Any substrate will affect graphene’s properties. Unfortunately, suspended graphene is unstable under scanning probe microscopy (SPM). The next best thing is to use a substrate that minimally changes graphene’s properties, while lending enough structure to prevent vibration during scans. A graphene substrate should have a large electronic band gap and no dangling bonds if it is to mimic "pure" graphene, said Decker. Suspended graphene is also very flat, which is a desirable substrate property.
A group based at Columbia University reported, in October 2010, that graphene supported on a boron nitride (BN) substrate had dramatically better electron mobility than graphene mounted on the most common semiconductor substrate, silicon dioxide (SiO2). However, the team’s macroscopic measurements couldn’t answer some fundamental research questions, said Yang Wang, co-lead author of the Nano Letters report. The Crommie and Zettl groups compared BN and SiO2 to find out why boron nitride was so inobtrusive. Scanning tunneling microscopy (STM) helped the researchers build up a picture of the substrate’s topography and measure its local electronic states.
In boron nitride’s hexagonal structure (h-BN), alternating nitrogen and boron atoms closely mimic the way carbon atoms are arranged in graphene. Boron and nitrogen atoms in BN compounds are paired equally, and together their valence electrons (three and five, respectively) equal those of a pair of carbon atoms (four each). Although the h-BN lattice is some 1.7% larger than graphene’s, the two honeycombs laid one on the other can be aligned much more closely than graphene and silicon dioxide. Unlike graphene, which normally has no band gap, h-BN has a wide band gap, due to the alternating boron and nitrogen atoms in its lattice. This could lead to graphene with a bandgap, which, while altering graphene’s properties, could lead to interesting applications.
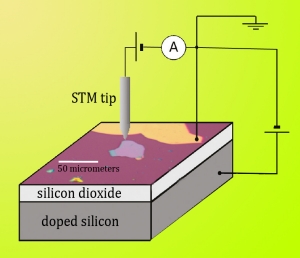 |
Figure 2. The Berkeley researchers deposited BN flakes on a layer of silicon dioxide, grown on a layer of doped silicon. The doped silicon was used as a gate electrode for doping the graphene during STM. Graphene was applied to both the boron nitride flakes (under the STM tip) and the bare silicon dioxide; the graphene (dark and light purple) was grounded by an electrode of gold/titanium (gold). The STM could scan across both substrate systems.
|
To create graphene/BN devices, Zettl’s group reduced boron nitride crystals to tiny flakes by exfoliating them between strips of Scotch Tape, then deposited the flakes onto a silicon dioxide layer grown on a layer of doped silicon. This method allowed the researchers to dope the graphene layer during STM.
The Crommie group’s Qiong Wu created graphene via chemical vapor deposition (CVD) on copper, which allows the carbon atoms to self-assemble into an atom-thick honeycomb lattice. The graphene sheets were then transferred from the copper to soft plastic and pressed onto the boron nitride flakes. The assembly was annealed at high heat. A layer of titanium gold electrode grounded the graphene.
Three graphene/BN systems were made for direct STM comparisons with graphene on silicon dioxide. Researchers measured topography and local charge concentrations at various doping levels determined by the silicon-layer gate electrode.
Boron nitride vs silicon dioxide
Atmospheric impurities in substrates alter graphene properties, shortening the electrons’ mean free path by creating "puddles." Charge puddles were notably absent from the BN substrate samples, said Victor Brar of the Crommie group. Practical graphene-based devices on BN substrates could be manufactured without the vacuum atmosphere that typically protects against water, air, and other impurities.
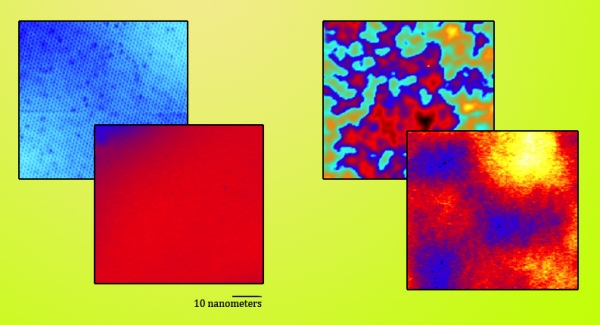 |
Figure 3. Measuring graphene on a boron nitride substrate (left), graphene on silicon dioxide (right). The STM mapped both topography (back) and local charge densities (front).
|
Dangling bonds (valence electron available for bonding with another atom) can mess with graphene properties as well. SiO2 has a high concentration of dangling bonds; boron nitride has none.
Topographically, graphene on boron nitride is much less rough than graphene on silicon, with height differences on the scanned surfaces reaching only around 40 picometers (trillionths of a meter). Height differences with the silicon dioxide substrate were up to 30 times greater.
Electronically, variations in charge density were reduced dramatically in the BN substrate, nearly unvarying.
The Crommie group investigated how electronic properties might vary according to the orientation of the graphene sheet on the boron nitride substrate. The two, not-quite-commensurate lattices betrayed their alignment by exhibiting changing moiré patterns with different orientations. Wang reports seeing many different alignments, including alignments that were "almost perfect," but no band gap.
The work recently appeared in Nano Letters: "Local electronic properties of graphene on a BN substrate via scanning tunneling microscopy," Régis Decker, Yang Wang, Victor W. Brar, William Regan, Hsin-Zon Tsai, Qiong Wu, William Gannett, Alex Zettl, and Michael F. Crommie, http://pubs.acs.org/doi/abs/10.1021/nl2005115.
After the Crommie and Zettl groups submitted their paper, related work by Xue et al appeared in Nature Materials, April 2011, available online at http://www.nature.com/nmat/journal/v10/n4/abs/nmat2968.html.
Visit Berkeley Lab’s website at http://www.lbl.gov/
Follow Small Times on Twitter.com by clicking www.twitter.com/smalltimes. Or join our Facebook group