February 28, 2011 — Various industries — such as aerospace, sporting goods manufacturers, construction – are incorporating technological advances using nanocomposites, with extraordinary results. Epoxy materials are being transformed into stiffer, lighter, and stronger materials thanks to the addition of fullerenes and carbon nanotubes (CNTs). Dongsheng Mao, Applied Nanotech, Applied Nanotech Holdings (APNT), describes a process involving multi-walled carbon nanotubes (MWCNTs) that have stronger mechanical properties yet remain lightweight and within end-product cost parameters.
These epoxy materials frequently appear in industry as fiber reinforced plastics (FRP). The properties of these new epoxy/carbon nanotube composites are generally not easily transferred to the FRP. However, using this new composite, APNT achieved a 31% improvement in the flexural strength of the final FRP and similar improvements are expected in compression strength.
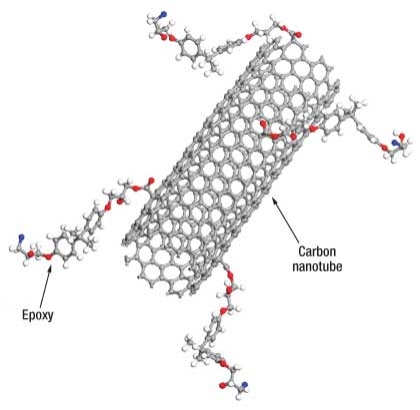 |
Figure 1. Schematic diagram of carbon nanotube (CNT) reinforced epoxy. Strong bonding between functionalized carbon nanotubes and epoxy is formed to significantly improve mechanical properties of the composites. |
The epoxy/CNT nanocomposite material has properties tailored to 3D assembling, thanks to an ability to uniquely handle blocks of CNTs. Large-volume applications include golf club shaft and sports racquet manufacture. Manufacturers using this material can decrease product weight while maintaining strength, portability, and flexibility. Sporting goods products are only the first application area.
The role carbon nanotubes play
Only 1-2% of the product is carbon nanotubes, yet they improve mechanical properties. By dispersing and functionalizing CNTs individually, ANI spread the CNTs throughout an epoxy matrix such that, when force is applied on the final product, a part of that stress is transferred to the CNTs.
CNTs possess unique mechanical properties. Their stiffness, strength and resilience exceed similar properties of any current material, with the potential for fundamentally new material systems, in particular, structural nanocomposites. Unfortunately, their integration with polymer matrices presents new technical challenges.
CNTs tend to aggregate with each other to form ropes or bundles due to intrinsic van der Waals forces associated with their high surface energy. De-agglomeration and dispersion of CNTs in various media has been recognized as one of the major challenges of commercial CNT adoption. Traditional methods such as sonication, high-shear mixing, stirring, and surfactants are often used in lab-scale quantities to disperse CNTs, but those methods have proven ineffective on an industrial scale. Although surface functionalization of CNTs has improved dispersions, the results for the mechanical properties of CNT-reinforced nanocomposites also depend on mixing procedures and carbon fiber-reinforced polymer (CFRP) manufacture methods.
Transferring interesting and unique nanocomposite properties to CFRPs can be realized only by successfully integrating functionalized CNTs into more complex structures. Using CNTs as a reinforcing component in polymer composites requires the ability to tailor the nature of the CNT walls to control the interfacial interactions between the CNTs and the polymer chains.
Applied’s CNT achieved over 40% improvement in both flexural and compression strength for epoxy/carbon nanotube composites. Chemical and mechanical modification and CNT functionalization, for them to be accepted and integrated properly into the epoxy matrix, were essential.
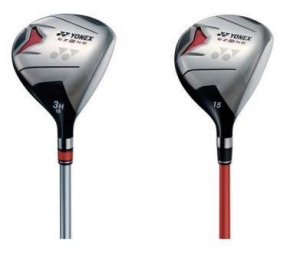 |
Figure 2. Yonex’s new golf clubs (EZONE) are made using Applied Nanotech, Inc’s patented technology (www.yonex.co.jp). |
Commercializing new CNT products
At times, companies worry about sharing propriety research information. Without all of the pertinent data, it is difficult to clearly understand how to apply nanotechnology methods to achieve the desired result. In cases like this, if the CNTs are not functionalized properly, or epoxy penetration into the fiber is suboptimal, the final material will have visible defects and no mechanical enhancement. Communication between industry and research entities is therefore essential to develop commercially viable products, as APNT demonstrates with this sporting goods partner.
Cost is always a manufacturing consideration. Even the greatest design improvements fail in the market if consumer cost is prohibitive. We advise clients to carefully examine how nanotechnology is applied to a project. In the past, single-wall nanotubes (SWCNTs) have enabled some great results, but costs were exorbitant. Today, functionalized CNT prices are dropping considerably, so we focused on MWCNTs. The results were significantly improved compression strength, flexural strength, modulus, impact strength, and vibration damping factor compared with epoxy.
We have demonstrated that the functionalization and dispersion methods used in CNT-reinforced epoxy and other thermosetting nanocomposites is a promising technology that can be expanded into many other fields, including aviation, defense, aerospace, marine, and cleantech.
Dongsheng Mao received his Ph.D from Chinese Academy of Sciences with a background of Materials Science and Engineering and is director of the Nanocomposite Division at Applied Nanotech. Inc., Applied Nanotech Holdings (Stock Symbol: APNT), 3006 Longhorn Blvd., Suite 107, Austin, TX 78758; [email protected]. Dongsheng Mao is director of Applied Nanotech Inc.’s Nanocomposite Division.
Follow Small Times on Twitter.com by clicking www.twitter.com/smalltimes. Or join our Facebook group